◆ 水泥工程技术
﹡新型干法水泥制造技术
本技术系在过去三十余年引进消化吸收国外水泥生产先进技术装备基础上,自主研发的成套全系列新型干法水泥技术。主要应用于水泥工业,可大幅降低水泥工业的能耗,对于水泥工业结构调整提供强有力的技术支撑,节能效果明显,达到世界先进水平。该技术成果已被应用于国内外百余条1000t/d—12000t/d规模的新型干法水泥生产线。

|
UCC10000t/d水泥生产线
|
﹡粉料制备技术
针对物料不同硬度、水分及特殊物性,加强系统耐磨蚀、抗粘堵性能,简化流程、降低能耗、提高效率,减少装备振动,延长配件使用期限,保证系统运行稳定可靠,使制备粉料产品符合各项指标要求。
公司研发的高海拔地区生料终粉磨系统,有效解决了高海拔地区由于气体密度减小、单位气体浮送能力降低而造成粉磨能力下降的问题,提高了粉磨效率,降低了粉磨能耗。
该成果在实际应用中取得了很好的效果,整个系统运行平稳,维修方便,综合技术指标达到国际先进水平。
﹡白水泥熟料成套技术
本技术是自主研发的成套白水泥技术及装备,最大单线白水泥熟料生产线可达到1500t/d规模,熟料烧成热耗、电耗均达到国际先进水平。
﹡高水分白垩制水泥新型干法技术
本技术在世界上首次成功解决了高水分白垩质原料储存、卸料易堵塞、难以精确计量、难以高效烘干、难以制备高合格率生料以及系统运转率低等技术难题,并且相对于传统的湿法煅烧和半干法煅烧工艺技术,具有低能耗、规模大型化和高运转率等优点。该技术在高水分白垩矿丰富的地区作为替代现存的湿法煅烧和半干法煅烧的先进技术,已在俄罗斯、白俄罗斯、哈萨克斯坦、多哥等国家数个新型干法水泥生产线中得到应用。

|
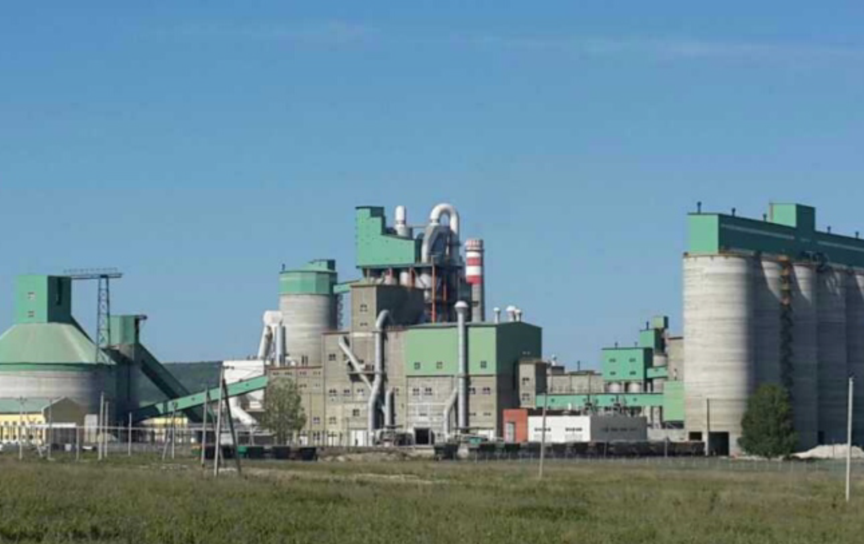
|
白俄罗斯国家水泥5000tpd生产线
|
俄罗斯宾萨亚洲水泥5000tpd生产线
|
﹡有害物旁路放风技术
本技术研发的低排灰立式和卧式两种旁路放风骤冷技术,可对富含氯、碱的原、燃料在水泥熟料煅烧系统中的应用提供成套解决方案,放风量可达50%;放风量每1%,热耗增加量不超过2.6kCal/kg熟料。该技术成果已被应用于国内外二十余条新型干法水泥生产线。
|
|
|

|
﹡高效快速烘干粉碎技术
|
|
本技术是集快速烘干与高效粉碎打散于一体的烘干粉碎技术。可对高水分、高粘性物料(如电石渣、白垩、活性硅酸钙滤饼、高水分泥灰岩等)进行快速烘干、高效粉碎,与水泥熟料生产线联产时,可大大节约热能,提高系统热能利用效率。本技术具有适应能力强、节能和高效、系统简单等诸多优点,现已广泛应用于建材、化工、电力、冶金等行业。
|
﹡带分级燃烧的低NOx预分解技术

|
|
本技术利用燃料分级技术对回转窑内产生的NOx进行快速还原,同时利用三次风分级技术抑制预分解系统内燃料燃烧时NOx的产生量,从而达到降低整个系统NOx排放的目的。在预分解系统采用烟煤时可实现50%的自脱硝效率。
|
﹡适应高硫燃料的水泥熟料煅烧技术
本技术利用水泥原料在高温下产生的活性CaO对气态SO2进行及时吸收,降低了S在熟料煅烧系统内的内循环量,使更多的S能被熟料固化带走,从而降低系统结皮堵塞的可能性。该技术可适应全硫含量高达6%的高硫燃料,并保证熟料烧成系统的可靠稳定运行,大大节省生产成本。
﹡生料立磨粉磨技术
本技术包括立磨磨内选粉和磨外选粉两种工艺系统技术。生料立磨磨内烘干选粉粉磨技术成功解决了水分高达20% 生料的烘干粉磨难题;生料立磨磨外烘干选粉粉磨技术,可适应水分小于12%原料,同时系统可比电耗可降低至13kW.h/t生料以内。该技术大大提升了立磨粉磨技术对原料水分的适应性和降低了系统电耗,有力推动了生料立
|
|
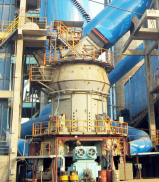
|
﹡水泥立磨终粉磨技术
本技术包括立磨磨内选粉和磨外选粉两种工艺系统技术。水泥立磨磨内选粉粉磨技术解决了料床稳定、颗粒整形、成品粒度分布、高效选粉和活性粉料喂料防堵等技术难题,系统可比电耗在27kW.h/t水泥左右。水泥立磨磨外选粉粉磨技术解决了磨外分选、成品粒度分布和磨内高效粉磨等技术难题,系统可比电耗在26kW.h/t水泥左右。
|
|
|
|
﹡终粉磨技术生料辊压机
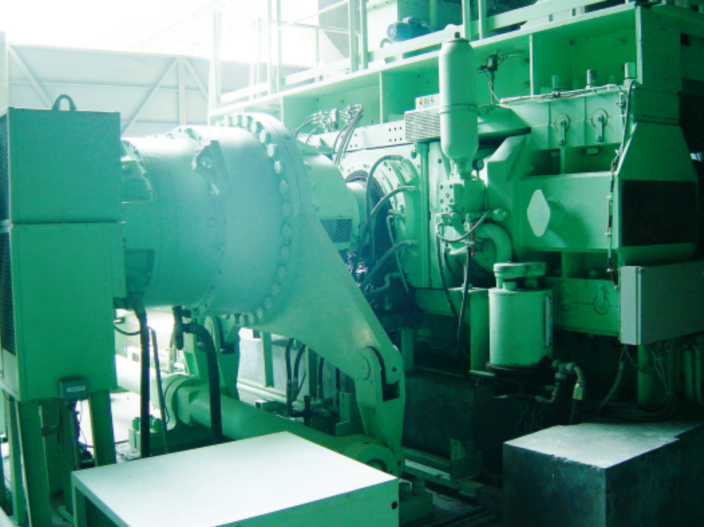
|
|
本技术充分发挥辊压机料床粉磨节能特点,在国内率先开发出高效烘干和高效分选的立式分选系统,不仅满足不同海拔地区粉料分选需求,且有效控制了生料质量,改善了生料易烧性。针对不同水分和不同易磨性物料研发的烘干分选系统和辊面耐磨技术,既保证了系统的长期稳定运行,也大幅提升了系统对原料的适应性,有力推动了生料辊压机终粉磨技术的发展。
|
﹡水泥辊压机半终粉磨技术
本技术是公司在水泥辊压机预粉磨、联合粉磨技术基础上,研究开发的新一代水泥粉磨技术,主要包括两选粉和三选粉半终粉磨两大系统。该技术在保证水泥成品质量前提下,充分发挥了辊压机高压料床粉磨的节能优势,同时解决了循环风机磨损等问题,降低粉磨系统可比电耗至26kW.h/t水泥以内,提高了系统运转率。
*三次风管摆动支撑技术
本技术利用摆动支座取代传统的滑动支座作为三次风管支撑系统中的中间支座。对安装角度偏差有更强的适应性,使现场安装更加简便;取消膨胀节,采用滑动密封装置补偿膨胀量,节省制造成本和维护成本,提高了可靠性;中间支架两端采用二力杆的铰支结构,优化结构受力,不会对底部基础产生弯矩,简化了土建基础,节省了工程投资并且简洁美观。
*大跨度落地式网架技术
本技术根据原料堆场屋盖系统跨度大,内部净空要求高的特点,开发设计落地式网架结构,以最大限度减小土建工程量,节约钢结构。网架落地,设计采光带,无窗户,提高堆场的密闭效果和采光效果。屋盖为半圆拱形,最大限度降低风荷载,减小积灰荷载,提高了内部空间利用率。
*大直径库顶网架结构
本技术解决了大直径、重荷载、高温复杂环境下库顶钢结构设计问题,有效避免了高温物料对结构的影响,避免了物料对结构构件的磨损,避免输送设备巨大拉力对库顶屋盖结构的影响。
*大直径筒仓超长预应力结构
本技术是针对直径60m以上大型筒仓,开发设计预应力结构,降低钢筋用量,提高施工效率,提高筒仓耐久性,最大限度增加预应力张拉间距,节约锚固墩混凝土量,减少锚具数量,减少张拉工程量,节省了工程投资。
*工厂智能化管理系统
本系统将工厂实际生产信息和运行数据通过安全防火墙从DCS控制系统中采集到信息化网络系统中,再对相关的数据进行处理,进行科学分析,自动生成各类分析报表,并将实时生产画面和实时生产信息通过网络展现给远端的技术专家和管理者面前,为技术专家远程处理问题或为管理者做出正确的决策服务。
*能源管理系统
本系统能对工厂的水、电、气、油等能源的使用进行有效控制,并通过对采集到的各种能源数据进行能耗分析,使管理者能够方便查看能源使用报表和分析报表,调整生产模式,计划下一步节能降耗的措施,从而减少能源消耗和使用成本,并能通过对数据的分析和对比,对部分设备进行重点控制,实现节能降耗。
*运动装置通信技术
现代水泥工厂中有很多运动设备(尤其堆取料设备)需要将信息传到中央控制室进行控制和监控,早期是通过大量的移动电缆进行信息传递,这种方式寿命短、操作复杂、维修量大且投资高,后期开始采用无线通讯模式传递信号,但由于工厂的环境恶劣,灰尘大,经常出现通讯闪断和不稳定现象,影响工厂正常生产。本技术通过规划多种无线通讯方案,在多个现场进行实地测试,并根据结果优化调整方案,确保了设备能在恶劣复杂的环境中长期稳定安全运行。
◆ 水泥工程技术拓展
﹡贫磁铁矿高压辊磨终粉磨及干式分选技术
本技术采用高压辊磨终粉磨系统,部分取代(也可完全取代)细碎和完全取代粗磨及细磨。高压辊磨机挤压后的物料通过机械分级和风力分级相结合的分选技术,分选出达到目标粒的铁矿粉,然后在不同粒度下通过磁选逐步提高至目标品位。本技术系统电耗相对于湿磨湿选技术降低约30%,耗水量降低约75%,尾矿矿浆量降低约75%,还能极大的降低系统钢耗。耗水量的大幅度降低和尾矿浆量的大幅减少,均可大幅度降低矿物处理的运行成本。
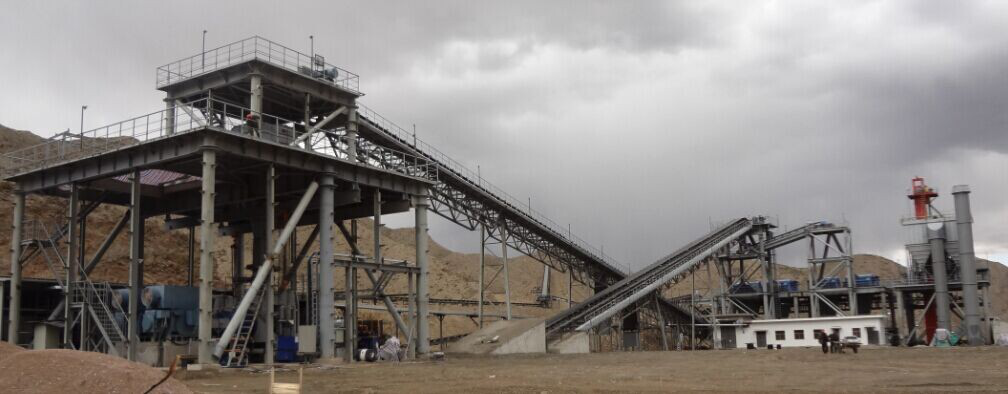
﹡新型干法窑煅烧氧化铝熟料技术
本技术利用新型干法水泥烧成技术原理,针对氧化铝熟料煅烧的特点,,专门研发可应用于赤泥、原铝土矿直接煅烧的氧化铝熟料新型干法煅烧技术。本技术可大大降低氧化铝熟料烧成热耗及系统电耗,较传统湿法窑煅烧工艺,降低热耗40%以上,降低电耗10%以上。
﹡活性石灰煅烧技术
本技术研发的活性石灰回转窑煅烧工艺及固定床预热器系统,使块状物料能充分吸收窑烟气内的热量,整个工艺过程简单,系统易于大型化。该技术煅烧的活性石灰,活性度大于90%,系统热耗低于1200kCal/kg,单线最大规模可达1500t/d。
﹡磷石膏制水泥联产硫酸技术
本技术主要是利用石膏中的钙质原料生产水泥熟料,其分解出来的气态硫则回收用于生产硫酸。长期以来,磷石膏作为一种工艺废弃物不能得到有效处理,目前在用的处理方案均不能对磷石膏进行大批量、大范围处置。采用本技术制备水泥和硫酸后,水泥熟料烧成热耗小于1250 kCal/kg.cl,烟气中SO2浓度(干基)小于9.5%,同时可使磷石膏得到规模化处置,减少其对环境的破坏。
◆ 绿色节能环保技术
﹡水泥窑纯低温余热发电技术
水泥生产中排出的废热主要是窑尾预热器出口和篦冷机多余的废气,从废热利用的角度应充分考虑提高回收效率,公司针对水泥窑废热的特点,结合系统配置和用户需求,可提供单压、双压、闪蒸等余热发电技术,遵循以热定电、节能减排的原则,充分利用可回收余热量,不额外增加系统热耗,综合考虑水泥熟料生产线的工艺流程、场地布置、供配电结构、供水设施等因素,合理制定技术参数,为用户提供简洁易行,便于操作管理,投资最省的系统,最大限度地利用水泥生产线窑头、窑尾余热资源。
公司的水泥窑余热发电技术经过工程应用及达标运营的实际检验,已经形成自身的技术模式和系列配套规模,可以为用户提供4.5MW、6MW、7.5MW、9MW、12MW、18MW的标准配置,并可根据现场条件及用户需求进行合理的调配和布置,同时还可提供系统调试、培训等服务,保证系统能够达到预定指标和优质运营效果。公司利用自身的优势已为十余条水泥生产线提供了总包、设计及服务,并为跨行业的余热利用提供了技术支持。
*电石渣制水泥规模化应用技术
本技术是依托“国家科技支撑计划”项目取得的研究成果。本技术针对传统电石渣制水泥工艺规模较小,技术经济指标差的现状,突破了新型干法电石渣制水泥的技术难关,实现了电石渣制水泥的规模化应用。主要工艺包括新型干法电石渣制水泥生料制备系统、电石渣烘干系统、预热预分解及回转窑煅烧工艺,均为针对电石渣的特点而开发,构成了新型干法电石渣制水泥的核心工艺。主要装备包括针对电石渣高湿、高粘性特点开发的烘干破碎机、高温动态选粉机、预热器及分解炉,并针对不同电石渣制水泥生产线的规模实现了配套系列化。
随着该技术的成功应用,获得了良好的示范效应,在全国范围内得到了快速的推广应用,目前该生产工艺已经成为PVC生产企业(电石法乙炔工艺)处置电石渣污染问题的标准配套工艺,已经主导了电石渣制水泥的发展方向。迄今公司已先后为十余条生产线提供了电石渣制水泥生产技术。
|
|
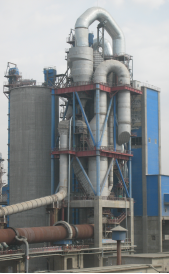
|
﹡水泥窑协同处置废弃物技术
本技术针对危险废弃物的多样性、复杂性、危险性等特点,成功开发了适宜水泥窑系统协同处置的危险废弃物协同处置工艺系统,其核心工艺系统主要包括危险废弃物预处理系统和水泥窑协同处置系统两部分。预处理系统针对危废多样性、复杂性和危险性的特点,通过集中储存、配伍、调质等工艺,完成危废的预处理。水泥窑协同处置系统,利用水泥窑固有的大热熔空间、高焚烧温度和长焚烧时间的特点,使危废中有机物彻底焚烧、无机重金属熔入水泥熟料晶格中,完成危废的彻底无害化处置,实现终端化处置,无二次处理问题,整体技术达国际先进水平。
*水泥窑协同处置废旧轮胎技术
本技术主要包括废旧轮胎多级破碎技术和废旧轮胎片的多点燃烧技术。通过多级破碎系统得到了粒径较小的轮胎碎片,缩短了轮胎的燃尽时间。废旧轮胎喂料方式由以前的整体入窑调整为经过计量后碎片入炉,并多点喂入。该技术可实现分解炉的燃料替代率达到30%,其替代率较直接喂入回转窑的方式提高了约1倍,且煅烧工况稳定,不会给系统带来其它不利影响,不会影响水泥熟料的产量和质量。
*建筑垃圾资源化利用技术
本技术针对我国建筑垃圾的特点,成功开发了建筑垃圾资源化处理技术,通过多级破碎、多粒径与多组分分选等工艺技术,完成建筑垃圾的精细化分离。其中废塑料、废木材等可作为替代燃料使用,碎石类可作为再生骨料,细粉类可用于砂浆制备、路基回填或水泥原料,废金属亦可实现回收,实现了资源化利用的最大化,整体技术达国际先进水平。
*矿/钢渣立磨粉磨技术
本技术根据料床粉磨原理,结合矿渣、钢渣特点,采用“对辊异化配辊”技术稳定料层,充分发挥辊压的潜能,提高粉磨效率,降低单位功率消耗;采用独创的磨内除铁、排铁技术,降低金属铁在磨内的富集程度;整个工艺系统实现全系统节点除铁,降低入磨矿渣、钢渣的铁含量,从而实现减少设备磨蚀,延长耐磨件寿命的目的。本技术利用立磨制备矿渣、钢渣微粉,系统电耗低于40kWh/t。